The concept and meaning of scale
When we talk about the word "scale", it covers a wide range of content. In the business and technical environment, "size" refers to factors such as organizational size, production capacity, and market coverage. For different types of businesses, size has very different effects.
Large enterprises often have significant advantages in resource allocation and market share. However, as the enterprise continues to expand, the complexity of management and coordination will also increase. In contrast, although small and medium-sized enterprises may lack the economic benefits brought by some economies of scale, they tend to show stronger competitiveness in terms of flexibility and innovation ability.
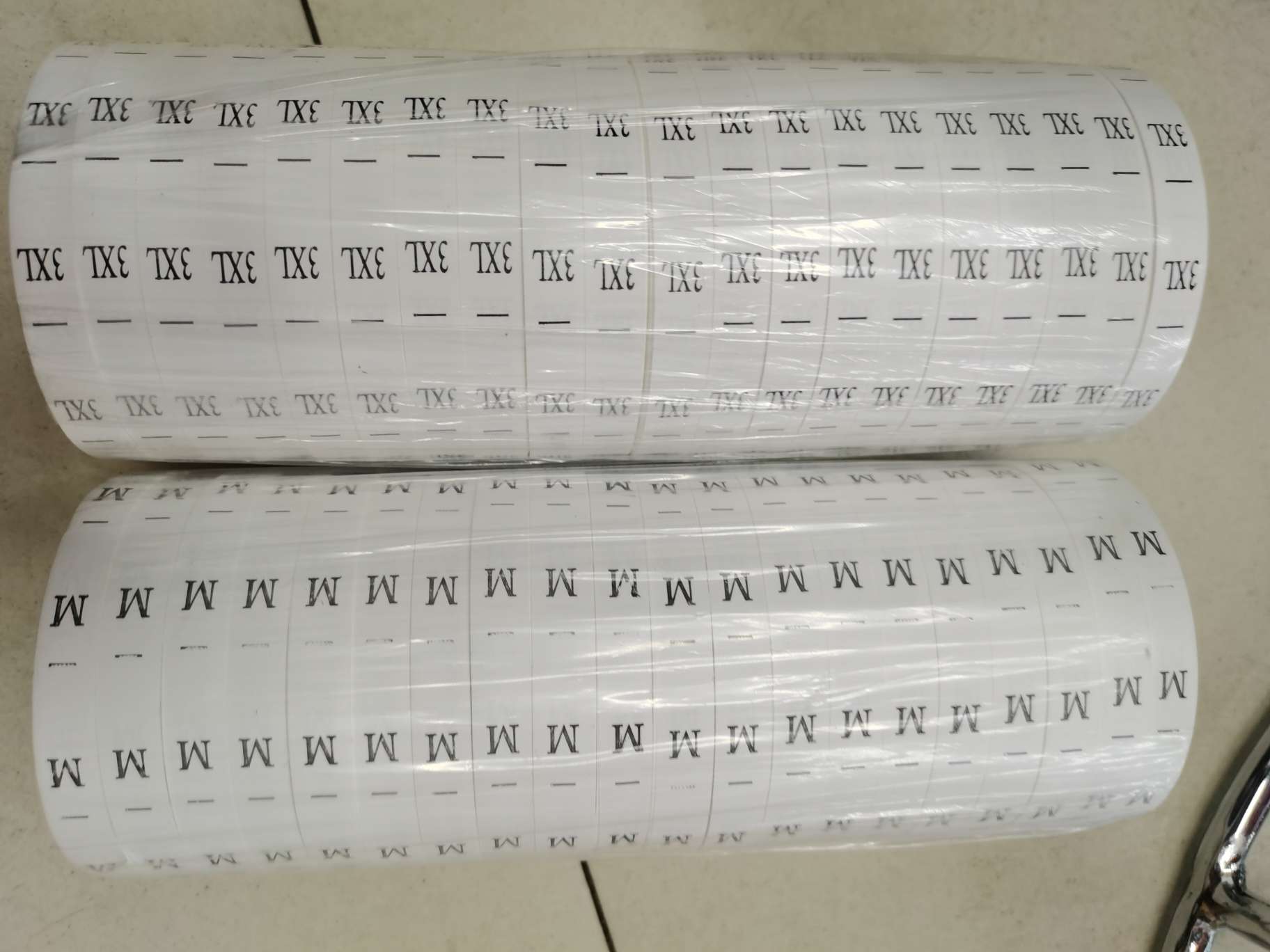
then, how to determine whether our business has reached the optimal scale? this requires us to comprehensively consider the data indicators of multiple dimensions and establish a complete set of evaluation methodology. By regularly reviewing these key performance indicators (KPIs), managers can make more informed strategic decisions.
Mechanism of job numbering
As an important tool, job numbering plays an indispensable role in many industries. Its core value is to simplify complex operational processes and increase the transparency of work. Whether it is batch tracking in the manufacturing industry or task allocation within the service industry, the rational use of job numbering can greatly improve work efficiency and service quality.
There are many types of job numbering systems on the market, each with its own specific application scenario. For example, bar code scanning technology, which is commonly used in the manufacturing field, enables accurate recording of the whole process from raw materials in storage to finished products out of storage, while in service-oriented enterprises, it relies more on spreadsheets or specialized software for work arrangement and progress monitoring.
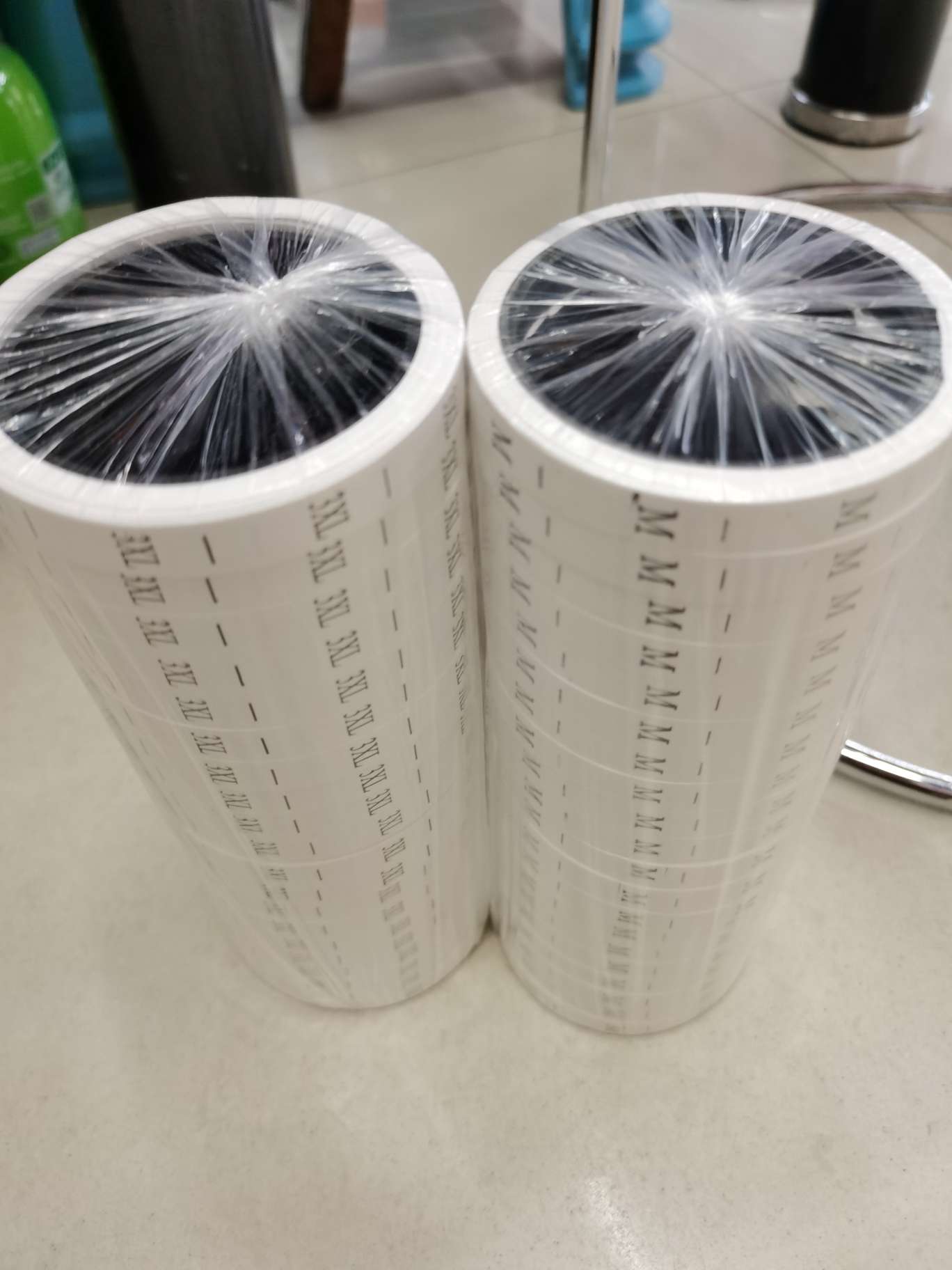
A good job numbering system not only promotes fine management, but also helps reduce operating costs. By accurately identifying each activity and forming a unified standard operation manual, employees can master the required skills in a short time, reducing training time and the chance of misoperation.
Scale Considerations in Project Management
A comprehensive project plan cannot be developed without a comprehensive measurement of the expected scale, the level of resource investment and the time frame. To ensure that the end result is delivered within established requirements and within budget, the project manager should be fully aware of the interrelationships between these three variables and their potential risks.
Estimating the right project size is a challenging task. Commonly used methods include trend prediction models based on historical data, Delphi methods and other quantitative analysis methods. Despite the advantages and disadvantages of each of the above methods, the common denominator is that they all require a large amount of reliable information as a supporting basis. In the event of a highly biased estimate, it may lead to many difficulties or even failures in the subsequent implementation phase.
Success stories show that proper upfront planning can bring great benefits. An Internet company once quickly adjusted its development roadmap because it accurately grasped the changes in market demand and launched a new product version six months in advance to seize the opportunity. On the contrary, another entrepreneurial team ignored the importance of the scale factor and was forced to give up midway when it encountered a capital chain break crisis in the later stage.
Fine operation in production process
Efficient production line operation mode depends on scientific and reasonable scale setting and rigorous and meticulous task coding. The advanced factory adopts the information management system to realize real-time monitoring of the status changes of each process, so as to ensure the consistency of product quality and the ability of on-time delivery.
For example, car manufacturers will flexibly allocate the number of production equipment and operating parameters according to the number of orders to maintain optimal capacity utilization. At the same time, each batch of products will be marked with a unique identification mark to trace the source information, and even if quality problems occur, the responsible department can be locked for rectification in the first place.
In addition, the use of IoT technology and big data platforms to collect feedback can further optimize the production process. Through continuous improvement and improvement of the existing system measures, not only can improve the level of customer satisfaction, but also for the future sustainable development has laid a solid foundation.
The Big View Behind Data Processing
Since entering the era of big data, the construction and maintenance of information management systems are facing unprecedented challenges. On the one hand, it is necessary to deal with the integration of massive heterogeneous data sources; on the other hand, it is necessary to take into account the requirements of security and compliance. To this end, it is particularly important to construct an effective classification identifier.
The "classification identifier" here actually means a job number in a broad sense. It can effectively serve the process of data analysis and mining. Especially in the face of large and disordered data sets, correct labeling allows researchers to quickly locate the object features of interest or the distribution of outliers, thus speeding up the problem-solving.
Of course, implementing strict access control under the premise of protecting users' personal privacy is also an essential part of the content. Only by doing this can we achieve the goal of intelligent transformation in a real sense-not only to protect sensitive data from being leaked out and cause damage, but also to make full use of the publicly available part to carry out innovative exploration and research work.
Practical Experience: From Theory to Practice
In order to let more colleagues benefit from the knowledge points provided in this article, we specially invited several professionals from different industries to share their personal experiences. Here is the story of one of the interviewees, Manager Li:
During a logistics distribution center renovation project I was in charge of, I initially encountered many bottlenecks, such as insufficient warehouse space, chaotic stacking of goods, and so on. Later, after the introduction of a modern warehouse management system with RFID RFID tags, these problems were solved.
now the layout of the entire site is compact and orderly, and all items can flow smoothly according to the predetermined path,
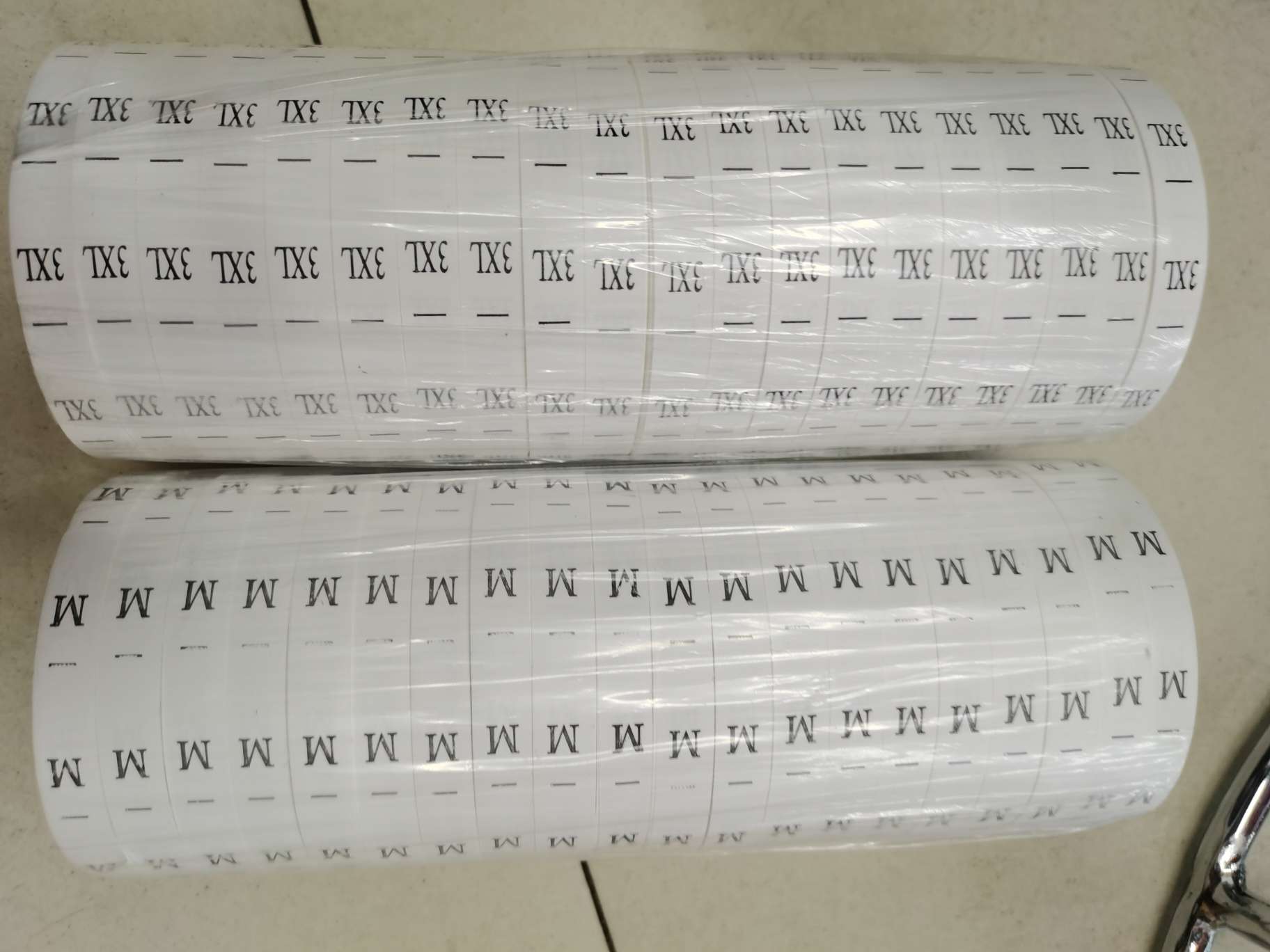